Water damage can severely affect insulated floor slabs, compromising their efficiency and structural integrity. Understanding how to prevent and address this issue is essential for maintaining a safe and energy-efficient home.
Water damage in domestic properties can cause serious issues, particularly when it occurs within insulated floor slabs. These integral components of modern home construction offer thermal efficiency, but when compromised by moisture, they can lead to structural and health problems.
This article discusses the construction of insulated floor slabs, the regulations surrounding their use, and the potential effects of water damage. We’ll explore how moisture is identified and addressed.
What is an Insulated Floor Slab?
An insulated floor slab is a type of concrete foundation that incorporates thermal insulation within its structure. The main purpose of the insulation is to prevent heat loss through the floor, which significantly improves the energy efficiency of a home. Insulated floor slabs are a critical feature of modern construction in colder climates where maintaining a consistent internal temperature is vital for energy conservation and comfort.
Building Regulations Mandating Insulated Floor Slabs
In regions like Northern Ireland, where energy efficiency is a priority, building regulations require that all new builds incorporate measures to reduce heat loss, including the use of insulated floor slabs.
These regulations are designed to meet high standards of energy performance and sustainability, which is particularly important given the climate. Insulation within the floor slab helps meet these standards by reducing the amount of energy needed to heat the property, ultimately supporting goals for reduced carbon emissions and lower energy costs.
The Building Regulations (Northern Ireland) 2012, particularly Technical Booklet F (Conservation of Fuel and Power), provide specific guidelines for insulated floor slabs. These regulations mandate minimum U-value requirements for floor insulation, which must typically be less than or equal to 0.25 W/m²K.
The regulations also include guidelines for proper installation of damp proof membranes and insulation to prevent moisture ingress and ensure effective thermal performance. Compliance with these standards contributes to reduced energy consumption, lower carbon emissions, and overall improved sustainability of domestic properties.
Building regulations ensure that homes are constructed with proper thermal protection, with a minimum required level of insulation. This results in better energy performance, a reduction in carbon emissions, and cost savings for homeowners.
The Typical Construction of a Concrete Floor Slab in a Domestic Property
A typical concrete floor slab in a domestic property consists of several layers:
- Sub-base: This is usually made of compacted hardcore or crushed stone and serves as a stable foundation for the slab.
- Damp Proof Membrane (DPM): A polythene sheet placed above the sub-base, laid on sand blinding, to prevent moisture from rising through the slab from the ground below.
- Thermal Insulation: This layer can sit above or below the concrete slab, reducing heat transfer between the ground and the interior of the property. Common materials used for this insulation include polystyrene boards or rigid polyurethane foam.
- Concrete Slab: The main structural component, this can be reinforced with steel mesh to provide strength and durability.
- Screed: A thin layer of cement, that creates a smooth, level surface for flooring materials like tiles, carpet, or hardwood.
Plumbing Located in the Slab
In many domestic properties, various types of plumbing are embedded within or beneath the insulated floor slab. This can include:
- Hot and Cold Water Pipes: These pipes distribute water to different areas of the home and can be embedded in the slab to reduce visible pipework.
- Underfloor Heating: Increasingly popular in modern homes, underfloor heating systems consist of water-filled pipes that circulate warm water beneath the floor surface to heat the property.
Causes of Water Leaks in the Slab
Pipes located within the slab are susceptible to damage and leaks. Several factors can contribute to this:
- Poor Installation: Inadequate installation of plumbing or underfloor heating systems can result in weak joints or connections that may eventually leak.
- Aging Materials: Over time, materials, such as copper, used in plumbing can degrade, increasing the likelihood of leaks.
- Ground Movement: Natural ground shifts, such as subsidence or settlement, can place stress on pipes, leading to cracks or breaks.
- Freezing Temperatures: In colder climates, pipes can freeze, especially if they are not properly lagged, causing them to expand and potentially burst.
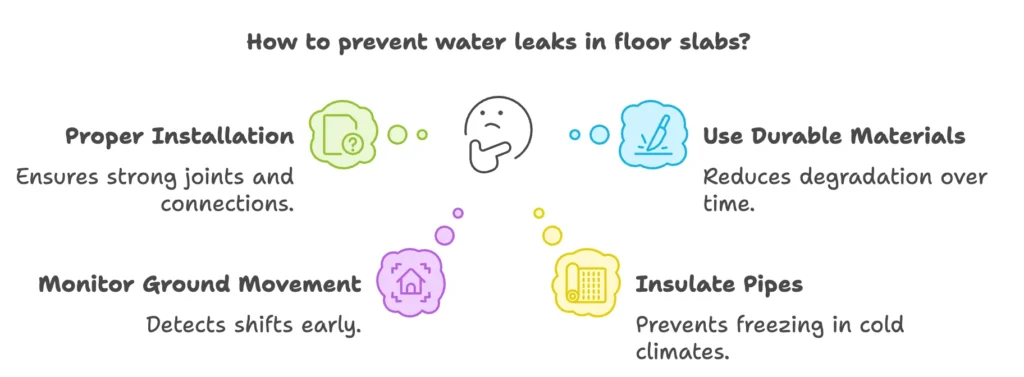
Identifying and Measuring Moisture in Insulated Floor Slabs
Signs of Water Damage
Water damage in insulated floor slabs can manifest in various ways, and homeowners should be vigilant for the following signs:
- Damp Spots on Floors: Localised wet areas or stains on the floor surface can indicate the presence of water within the slab.
- Mould Growth: Mould can develop in damp environments, especially in areas with poor ventilation, and is often a key indicator of excess moisture.
- Musty Odours: The smell of dampness is often noticeable before visible signs appear, especially in enclosed spaces.
- Cracking or Lifting Flooring: Water can weaken the adhesive bond between the slab and the flooring material. Moisture under tiled flooring can cause tiles to become loose or break, while wooden floors may absorb water, resulting in warping, swelling, or ‘cupping’ of the planks. Both scenarios can lead to an uneven floor surface and require repair or replacement of the affected materials.
- Low Level wall plaster: Water leaking from a pipe will often spread out across the slab and, when it has nowhere else to go, rise up into the walls through capillary action. This can lead to damage to the wall plaster, which will manifest as damp patches, discoloration, and potential crumbling of the plaster over time.
Methods for Measuring Moisture
Several tools and techniques are available for detecting and measuring the extent of moisture within an insulated floor slab:
- Moisture Meters: These handheld devices can detect the presence of moisture within the slab by measuring the electrical resistance of the material.
- Thermal Imaging Cameras: These cameras detect differences in surface temperature, which can help identify areas where moisture may be present.
- Relative Humidity Sleeves: These sleeves are inserted into pre-drilled holes in the concrete slab to measure the internal relative humidity. This method provides the most accurate assessment of the moisture levels within the slab, which helps identify hidden water issues that may not be apparent from surface-level observations.
Addressing Water Damage in Insulated Floor Slabs
Assessing the Extent of the Damage
Once water damage is detected, a thorough assessment of the extent of the problem is essential. This can involve:
- Inspecting the Plumbing: Identifying the source of the leak is critical before any repair work begins. This might involve pressure testing the pipes or using specialist cameras to inspect the plumbing network.
- Surveying the Insulation: If the insulation within the slab has become saturated, it may need to be removed and replaced to prevent further heat loss and damage to the structure. Wet insulation loses its thermal effectiveness, leading to increased energy costs and a potential drop in indoor comfort levels. Additionally, prolonged moisture can foster mould growth within the insulation, posing health risks.
- Evaluating the Structural Integrity: Prolonged exposure to moisture can weaken the concrete, and a structural engineer may need to assess whether the slab is still sound.
Best Practices for Rectification
The process for repairing water damage in insulated floor slabs varies based on severity and includes several key methods:
1. Isolating the Source of the Leak
The first step is to stop the water at its source, usually by repairing or replacing the damaged plumbing. If the leak is minor, it might be possible to fix the issue by repairing joints or sealing cracks. However, more severe cases may require replacing entire sections of pipe.
2. Drying the Insulation
Once the leak has been stopped, drying the insulation is crucial. Standard dehumidifiers and fans may help reduce surface moisture, but they are often insufficient for insulation deep within the slab. Injection drying, which involves injecting heated air through drilled holes, is necessary to effectively target and dry the insulation. This method ensures complete moisture removal, restores thermal properties, and prevents long-term damage and mould growth. It requires removal of in-situ floor coverings to be effective.
3. Drying the Slab
Drying the slab itself is also essential. Injection drying can effectively target moisture within the slab by injecting heated air through drilled holes. However, standard dehumidifiers and air movers are also needed to manage ambient moisture levels and ensure complete drying. These methods work together to remove moisture from both the surface and internal layers of the slab, helping restore its structural integrity and preventing further damage.
4. Repairing the Slab and Floor Coverings
Once the slab and insulation have been dried, any structural damage to the concrete can be repaired. This may involve filling cracks or applying a new layer of screed. Finally, the floor coverings can be replaced, whether that involves reinstalling the original materials or laying new ones.
Conclusion
Water damage to insulated floor slabs in domestic properties can have serious implications, both structurally and financially. The combination of modern insulation materials and concrete slabs provides significant thermal benefits, but when compromised by leaks, the situation can quickly escalate. Early identification of moisture, accurate assessment of damage, and swift rectification are essential to mitigate these issues.
Understanding the importance of the slab’s construction, the potential causes of leaks, and the methods of repair can help homeowners and professionals alike address problems effectively. Water damage in insulated floor slabs can be resolved, ensuring the long-term safety and energy efficiency of the property.